Fiber Cement Insulated Siding
Fiber cement insulated siding represents a significant advancement in exterior cladding, offering a compelling blend of durability, energy efficiency, and aesthetic appeal. This guide delves into the multifaceted nature of this material, exploring its composition, installation, maintenance, cost-effectiveness, environmental impact, design versatility, and fire safety features. We aim to provide a thorough understanding of fiber cement insulated siding, empowering homeowners and professionals alike to make informed decisions.
From its manufacturing process and thermal properties to its long-term cost implications and aesthetic possibilities, we will examine every aspect of this increasingly popular siding option. We will also compare it to other common siding materials, highlighting its unique advantages and disadvantages. This comprehensive overview will equip you with the knowledge necessary to determine if fiber cement insulated siding is the right choice for your next project.
Material Composition and Properties
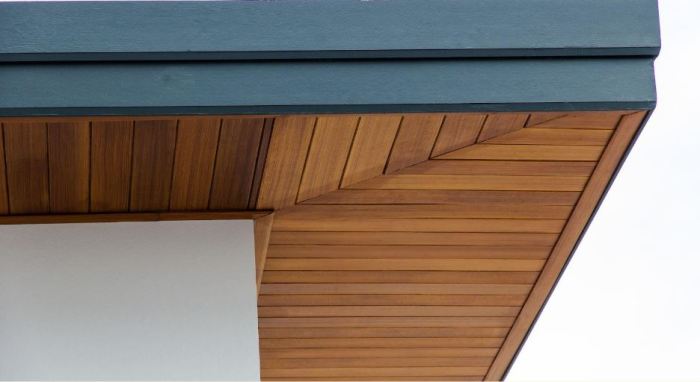
Fiber cement insulated siding offers a compelling blend of aesthetics, durability, and energy efficiency. Its composition and manufacturing process contribute significantly to its superior performance compared to traditional siding materials. Understanding these aspects is crucial for making informed decisions regarding exterior home improvements.
Typical Components of Fiber Cement Insulated Siding
Fiber cement insulated siding typically consists of a cement-based core reinforced with cellulose fibers. This core provides structural strength and fire resistance. An insulating layer, often made of expanded polystyrene (EPS) or polyurethane foam, is bonded to the cement core, enhancing the siding’s thermal performance. Finally, a protective outer layer, usually a factory-applied finish coat, provides weather resistance and aesthetic appeal.
The specific composition and thickness of each layer can vary depending on the manufacturer and product specifications. This layered construction distinguishes fiber cement insulated siding from traditional fiber cement siding, which lacks the integrated insulation.
Manufacturing Process of Fiber Cement Insulated Siding
The manufacturing process involves several key steps. First, a slurry of cement, cellulose fibers, and water is mixed and formed into panels. These panels are then cured under controlled conditions to achieve the desired strength and density. Next, the insulating layer is applied to one side of the cured panel, often using a bonding adhesive. Finally, a protective finish coat is applied, which can be painted or stained to achieve the desired color and texture.
The entire process is highly automated to ensure consistent quality and performance. Precision and quality control are vital throughout the process to ensure the final product meets stringent performance standards.
Thermal Performance of Fiber Cement Insulated Siding
Fiber cement insulated siding significantly outperforms many other siding materials in terms of thermal performance. Its integrated insulation layer effectively reduces heat transfer, leading to lower energy consumption for heating and cooling. Compared to traditional wood siding, which offers minimal insulation, fiber cement insulated siding boasts significantly higher R-values (a measure of thermal resistance). Similarly, it surpasses vinyl and aluminum siding, which have relatively low R-values.
The improved insulation contributes to a more comfortable indoor environment and lower utility bills, making it a cost-effective long-term solution. For example, a home with fiber cement insulated siding might experience a 15-20% reduction in energy costs compared to a home with traditional wood siding, depending on climate and other factors.
Moisture Resistance Properties of Fiber Cement Insulated Siding
Fiber cement insulated siding exhibits excellent moisture resistance. The cement core is inherently resistant to water damage, rot, and insect infestation, unlike wood siding. The protective outer layer further enhances this resistance, shielding the underlying components from moisture penetration. The integrated insulation layer also helps to prevent moisture buildup within the wall assembly, reducing the risk of mold and mildew growth.
Proper installation, ensuring adequate ventilation and drainage, is crucial to maintaining the siding’s moisture resistance. This inherent resistance contributes to the longevity and structural integrity of the siding, minimizing the need for costly repairs or replacements.
Durability Comparison of Siding Materials
Material | Lifespan (Years) | Resistance to Pests/Rot | Maintenance |
---|---|---|---|
Fiber Cement Insulated Siding | 50+ | Excellent | Low |
Wood Siding | 15-30 | Poor to Fair | High |
Vinyl Siding | 20-40 | Excellent | Low to Moderate |
Aluminum Siding | 30-50 | Excellent | Low |
Installation and Maintenance
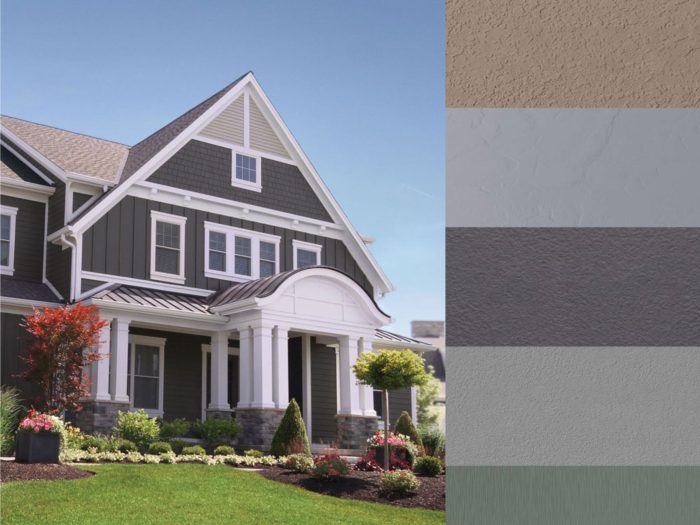
Fiber cement insulated siding offers a durable and energy-efficient exterior cladding solution. Proper installation and regular maintenance are crucial to maximizing its lifespan and performance. This section details the process of installation, addresses potential challenges, and provides guidance on maintaining the siding’s aesthetic appeal and structural integrity.
Step-by-Step Installation Guide
Installing fiber cement insulated siding requires careful planning and execution. The process typically involves several key steps, from preparation to finishing. Following these steps meticulously will ensure a successful and long-lasting installation.
- Preparation: Begin by thoroughly cleaning the existing wall surface, removing any loose paint, debris, or damaged materials. Ensure the framing is structurally sound and level. This foundational step is crucial for proper siding adhesion and overall project success.
- Sheathing Installation (if necessary): If the existing wall sheathing is inadequate, install appropriate sheathing to provide a stable and even surface for the siding. This might involve plywood or OSB, depending on local building codes and project requirements.
- Water-Resistive Barrier: Apply a water-resistive barrier (WRB) over the sheathing to protect the wall assembly from moisture intrusion. Overlap seams properly and seal them with appropriate tape to maintain a continuous barrier. This step is critical in preventing water damage.
- Siding Installation: Start at a corner or a pre-determined starting point and install the siding panels according to the manufacturer’s instructions. Use appropriate fasteners and ensure proper spacing and alignment. Maintain consistent overlaps and ensure a tight seal at all joints.
- Flashing and Trim: Install flashing around windows, doors, and other penetrations to prevent water leakage. Install trim pieces to finish the edges and corners of the siding. Proper flashing and trim work is essential for a watertight installation.
- Caulking and Sealing: Seal all joints, seams, and penetrations with high-quality exterior-grade caulk to prevent water and air infiltration. Pay particular attention to areas around windows, doors, and corners. This step helps maintain the building’s energy efficiency and protects against moisture damage.
Common Installation Challenges and Solutions
Several challenges can arise during fiber cement insulated siding installation. Addressing these proactively minimizes potential problems and ensures a successful outcome.
- Improper Fastener Placement: Using incorrect fasteners or improper spacing can lead to cracking or damage. Solution: Use the manufacturer-recommended fasteners and spacing to ensure proper support and prevent damage.
- Moisture Intrusion: Inadequate flashing or sealing can result in water damage. Solution: Ensure proper flashing and sealing around all penetrations and joints. Use high-quality, weather-resistant materials.
- Uneven Surfaces: Installing siding on uneven surfaces can lead to gaps and misalignment. Solution: Prepare the surface properly, ensuring it is level and smooth before installation. Use shims if necessary to correct minor imperfections.
- Incorrect Cutting and Fitting: Improper cutting techniques can result in damaged panels or poor fit. Solution: Use appropriate cutting tools and techniques to ensure clean cuts and precise fitting of panels. Utilize a professional if necessary.
Best Practices for Maintaining and Cleaning Fiber Cement Insulated Siding
Regular cleaning and maintenance extend the lifespan and preserve the appearance of fiber cement insulated siding.
Cleaning should be performed at least once or twice a year, using a solution of mild detergent and water. A soft-bristled brush or sponge is recommended to avoid scratching the surface. Power washing should be done with caution, using a low-pressure setting to prevent damage. Avoid using abrasive cleaners or harsh chemicals, as these can damage the siding’s finish.
Regular inspections for any signs of damage, such as cracks or loose panels, should also be conducted.
Preventative Maintenance Schedule for Fiber Cement Insulated Siding
Task | Frequency | Description |
---|---|---|
Visual Inspection | Annually | Check for cracks, loose panels, or damage. |
Cleaning | Semi-annually | Clean with mild detergent and water. |
Caulk Inspection and Repair | Annually | Inspect and replace any damaged or deteriorated caulking. |
Flashing Inspection | Every 2-3 years | Inspect flashing around windows and doors for damage. |
Inspection Checklist for Damage
A thorough inspection is crucial for early detection of potential problems. This checklist aids in a systematic review.
- Inspect all panels for cracks, chips, or other damage.
- Check for loose or missing fasteners.
- Examine caulking and sealant for cracks or gaps.
- Inspect flashing around windows and doors for damage or deterioration.
- Look for signs of water damage, such as discoloration or swelling.
- Check for any signs of insect infestation.
Cost and Lifespan
Fiber cement insulated siding presents a compelling option for homeowners seeking a durable and energy-efficient exterior cladding. However, understanding the associated costs and lifespan is crucial for making an informed decision. This section will delve into a comparative analysis of initial costs, long-term expenses, lifespan estimations, and return on investment calculations to help you weigh the financial aspects of this siding choice.
Initial Cost Comparison
The initial cost of fiber cement insulated siding is generally higher than that of vinyl or aluminum siding, but often lower than options like brick or stone. Prices vary based on factors such as the chosen style, thickness, and installation complexity. For example, a basic fiber cement insulated siding installation might cost between $8 and $15 per square foot, while premium options can exceed $20 per square foot.
Vinyl siding, in contrast, typically ranges from $3 to $8 per square foot, while brick can easily reach $20 to $40 per square foot or more. These figures include materials and professional installation. It’s important to obtain multiple quotes from reputable contractors to accurately assess costs in your specific area.
Long-Term Cost Considerations
While the initial investment is significant, fiber cement insulated siding offers substantial long-term cost savings. Its durability reduces the need for frequent repairs and replacements, unlike some less durable alternatives. Low maintenance requirements translate to lower ongoing expenses. The superior insulation properties contribute to reduced energy bills, further offsetting the initial cost over time. Potential repair costs might include replacing damaged panels due to accidental impact or addressing minor weathering issues.
However, the robust nature of the material typically minimizes such occurrences.
Lifespan Estimates Under Varying Climates
The lifespan of fiber cement insulated siding is impressive, generally estimated to be between 50 and 80 years. However, this longevity can be influenced by climatic conditions. In regions with harsh winters, extreme temperature fluctuations, or frequent exposure to strong winds and heavy precipitation, the siding might require slightly more frequent maintenance or show signs of wear earlier than in milder climates.
For instance, areas prone to heavy snowfall might experience occasional minor damage from ice buildup, requiring prompt attention. Conversely, in dry, sunny climates, the siding’s lifespan is expected to approach the higher end of the estimated range.
Return on Investment (ROI) Calculation
Calculating the ROI for fiber cement insulated siding involves comparing the total cost of ownership over its lifespan to the cost of alternative materials. This calculation should include the initial purchase price, installation costs, projected maintenance expenses, and potential energy savings. For example, consider a 1,000 square foot house. If fiber cement siding costs $12,000 to install and saves $500 annually on energy bills over 50 years, the total energy savings would be $25,000.
Subtracting the initial cost, this results in a net positive return of $13,000. This is a simplified calculation and should be adjusted based on specific costs and energy savings in your region. A more detailed ROI analysis would involve considering the potential resale value increase associated with this high-quality siding.
Total Cost of Ownership Comparison (20 Years)
Material | Initial Cost | Maintenance (20 years) | Total Cost (20 years) |
---|---|---|---|
Fiber Cement Insulated | $12,000 – $20,000 | $1,000 – $2,000 | $13,000 – $22,000 |
Vinyl | $4,000 – $8,000 | $2,000 – $4,000 | $6,000 – $12,000 |
Aluminum | $5,000 – $10,000 | $1,500 – $3,000 | $6,500 – $13,000 |
Brick | $20,000 – $40,000 | $500 – $1,000 | $20,500 – $41,000 |
Note: These figures are estimates and can vary based on location, project size, and material choices. It’s crucial to obtain accurate quotes for your specific project.
Environmental Impact
Fiber cement insulated siding presents a complex environmental profile, encompassing manufacturing processes, material sourcing, lifespan, and eventual disposal. Understanding its complete environmental impact requires a balanced assessment of its advantages and disadvantages compared to alternative building materials. This section will explore the key aspects of the environmental footprint of fiber cement siding.
Manufacturing Process and Resource Consumption
The manufacturing of fiber cement siding involves several steps, each with its own environmental implications. Cement production, a significant component, is energy-intensive and releases greenhouse gases, primarily carbon dioxide (CO2). The sourcing of raw materials, including Portland cement, cellulose fibers (often from recycled wood pulp), and silica sand, also contributes to the overall environmental impact. Transportation of these materials to the manufacturing facility and the finished product to construction sites adds to the carbon footprint.
However, the use of recycled materials in the manufacturing process can mitigate some of these negative impacts. For example, the incorporation of recycled wood fibers reduces reliance on virgin timber, conserving forest resources and reducing deforestation.
Recyclability and Disposal
Fiber cement siding is not readily recyclable in the same way as some other materials. While some components can be potentially recovered and reused in other applications, the process is not widely established. Disposal typically involves landfilling, which contributes to the overall waste stream. However, the durability and long lifespan of fiber cement siding mean that it does not need frequent replacement, reducing the frequency of disposal compared to materials with shorter lifespans.
Embodied Carbon Compared to Other Siding Materials
The embodied carbon of fiber cement siding, representing the total greenhouse gas emissions associated with its production, transportation, and installation, varies depending on the specific product and manufacturing process. While it generally has a higher embodied carbon than some other siding materials like vinyl, it often demonstrates a lower embodied carbon footprint than materials such as wood, especially when considering the sourcing and transportation of lumber from distant forests.
Life-cycle assessments (LCAs) are crucial for accurate comparisons between different siding options, as they account for the entire lifespan of the product. These LCAs should consider factors like energy consumption during manufacturing, transportation distances, and the durability of the material.
Sustainability Certifications and Eco-labels
Some manufacturers of fiber cement siding pursue sustainability certifications and eco-labels to demonstrate their commitment to environmentally responsible practices. These certifications may validate aspects of the production process, such as the use of recycled materials, energy efficiency, and responsible sourcing of raw materials. Consumers should look for such certifications when selecting fiber cement siding to help ensure that their purchase aligns with their sustainability goals.
Examples of relevant certifications might include those related to sustainable forestry or responsible manufacturing practices, although specific certifications vary by region and regulatory body.
Environmental Benefits and Energy Savings
Despite its manufacturing impacts, fiber cement siding offers several environmental benefits. Its durability and long lifespan significantly reduce the need for frequent replacements, minimizing waste and resource consumption over time. Furthermore, its inherent insulating properties contribute to improved energy efficiency in buildings. This reduced energy consumption translates to lower greenhouse gas emissions associated with heating and cooling, thus offsetting some of the embodied carbon.
The long-term energy savings from reduced heating and cooling loads can contribute to a smaller overall carbon footprint compared to less energy-efficient siding options over the building’s lifetime. A well-insulated home reduces reliance on fossil fuels for energy production, which can have significant positive environmental implications.
Design and Aesthetics
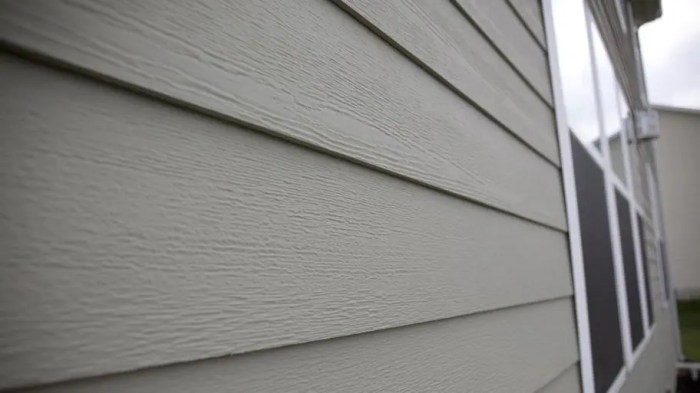
Fiber cement insulated siding offers a compelling blend of durability and aesthetic appeal, providing homeowners with a wide range of options to enhance their home’s exterior. Its versatility allows for seamless integration into various architectural styles, creating a visually stunning and long-lasting façade. The material’s inherent properties contribute to a clean, modern look while also allowing for the replication of traditional styles.
Color and Texture Options
Fiber cement siding is available in a broad spectrum of colors and textures, mimicking the appearance of natural materials like wood, stone, and stucco. Manufacturers utilize advanced coloring techniques to ensure long-lasting vibrancy and resistance to fading. Popular color palettes range from classic earth tones to contemporary grays and blues, offering homeowners considerable flexibility in choosing a color scheme that complements their home’s style and the surrounding landscape.
Textures vary from smooth, sleek finishes to deeply embossed patterns that add depth and visual interest. Some manufacturers offer options that closely replicate the look of wood grain, providing the aesthetic appeal of natural wood without the maintenance challenges.
Design Styles that Complement Fiber Cement Siding
Fiber cement siding’s adaptability makes it suitable for a wide array of architectural styles. Its clean lines and versatility work well with modern, contemporary, and farmhouse designs. The ability to mimic other materials allows it to integrate seamlessly into traditional styles like Victorian, Colonial, and Craftsman homes. The siding’s durability also makes it a suitable choice for rustic or coastal designs, where it can withstand harsh weather conditions.
Architectural Applications of Fiber Cement Siding
Fiber cement insulated siding is particularly well-suited for homes in diverse climates and architectural settings. Its resistance to moisture, insects, and fire makes it ideal for coastal regions prone to hurricanes and areas with high humidity. Its durability and low maintenance requirements make it a cost-effective solution for large-scale residential projects, such as apartment complexes or townhouses. Furthermore, its ability to mimic various materials allows it to seamlessly blend into established neighborhoods with diverse architectural styles.
Integrating Fiber Cement Siding into Different Home Designs
The integration of fiber cement siding into various home designs requires careful consideration of color, texture, and trim details. For a modern home, a sleek, smooth finish in a neutral color like gray or white might be chosen, complemented by minimalist trim. A farmhouse style home could benefit from a textured finish that mimics wood, paired with darker trim and contrasting accents.
Traditional homes could utilize siding that replicates brick or stone, creating a classic and timeless look. The choice of accessories, such as shutters and window frames, also plays a significant role in the overall aesthetic.
Visual Representations of Fiber Cement Siding on Various House Styles
Imagine a sleek, modern two-story home with clean lines and large windows. The exterior is clad in smooth, charcoal gray fiber cement siding, creating a sophisticated and contemporary look. Minimalist black trim accentuates the windows and doors, while a small, strategically placed planter adds a touch of greenery.
Picture a charming Craftsman bungalow, its exterior adorned with fiber cement siding that replicates the warm tones and texture of natural wood. The siding’s rich brown hue complements the home’s exposed beams and overhanging eaves, creating a cozy and inviting atmosphere. Dark brown trim and a stone foundation further enhance the traditional aesthetic.
Envision a spacious Victorian home with intricate detailing and a steeply pitched roof. The exterior is clad in fiber cement siding that mimics the appearance of light-colored brick, creating a classic and elegant look. White trim and decorative brackets accentuate the home’s architectural features, resulting in a timeless and refined aesthetic.
Consider a rustic farmhouse, its exterior showcasing fiber cement siding with a deeply embossed texture that replicates the look of aged wood. The siding’s warm, earthy tones complement the home’s stone foundation and large, inviting porch. Dark brown trim and strategically placed landscaping further enhance the rustic charm.
Visualize a coastal cottage, its exterior protected by durable, light gray fiber cement siding that withstands the elements. The smooth finish complements the home’s simple design and large windows, offering a clean and airy feel. White trim and a light blue door add a touch of coastal charm.
Fire Resistance and Safety: Fiber Cement Insulated Siding
Fiber cement insulated siding offers a significant advantage in terms of fire safety, contributing to the overall fire resistance of a building. Its inherent properties and composition make it a superior choice compared to many other siding materials, providing a crucial layer of protection against fire spread.Fiber cement siding’s fire-resistant properties stem from its composition, primarily a mixture of cement, cellulose fibers, and other additives.
The cement acts as a fire retardant, resisting ignition and slowing the spread of flames. The cellulose fibers, while combustible, are embedded within the cement matrix, limiting their ability to contribute to rapid fire spread. This combination results in a material that is non-combustible or has a very high resistance to burning.
Fire Ratings of Fiber Cement Siding Compared to Other Materials
Fiber cement siding typically achieves a Class A fire rating, the highest classification for fire resistance in building materials. This means it offers superior protection against fire spread compared to many other siding options. For instance, vinyl siding is often classified as Class C, indicating significantly lower fire resistance. Wood siding, while aesthetically pleasing, presents a considerable fire risk and typically does not achieve a Class A rating without significant fire-retardant treatments.
The superior fire resistance of fiber cement contributes to a safer building environment and potentially lower insurance premiums.
Safety Precautions During Installation and Maintenance
While fiber cement siding is inherently fire-resistant, standard safety precautions are still necessary during installation and maintenance. Proper use of personal protective equipment (PPE), including safety glasses, gloves, and respirators, is crucial to prevent inhalation of dust and potential injury from sharp edges. Following the manufacturer’s instructions for cutting and handling the siding is also essential. When using power tools, care should be taken to avoid sparks or accidental ignition, particularly near combustible materials.
Regular inspection of the siding for damage is recommended to ensure its continued fire-resistant properties. Damaged sections should be repaired or replaced promptly.
Building Codes and Regulations in Fire-Prone Areas
Building codes and regulations often mandate or strongly recommend the use of fire-resistant materials in areas prone to wildfires or with stringent fire safety requirements. Fiber cement siding’s Class A fire rating often satisfies these regulations, making it a suitable choice for construction in such high-risk areas. Local building departments should be consulted to determine specific requirements and ensure compliance with all applicable codes.
In some jurisdictions, the use of Class A rated siding might be mandatory for new construction or renovations in designated fire zones. This demonstrates the significant role fiber cement siding plays in meeting regulatory standards for fire safety.
Contribution to Overall Building Fire Safety
Fiber cement insulated siding contributes to overall building fire safety in several ways. Its inherent fire resistance prevents or slows the spread of flames across the exterior walls, providing crucial time for evacuation and firefighter response. This fire-resistant barrier also helps protect the building’s structure and interior from fire damage, potentially minimizing losses. The added insulation provided by some fiber cement siding products can also improve the building’s overall thermal performance, potentially reducing the risk of overheating that could contribute to fire ignition.
The combination of fire resistance and thermal protection contributes to a safer and more secure building environment.
Query Resolution
What is the best way to clean fiber cement insulated siding?
Regularly cleaning with a soft brush, mild detergent, and water is recommended. Avoid pressure washing, which can damage the surface.
Can fiber cement insulated siding be painted?
Yes, it can be painted, but it’s crucial to use a paint specifically designed for fiber cement siding to ensure proper adhesion and longevity.
Does fiber cement insulated siding attract pests?
Fiber cement siding is generally resistant to pests, unlike wood siding, offering a significant advantage in terms of maintenance and longevity.
How long does it take to install fiber cement insulated siding?
Installation time varies depending on the size of the project and the experience of the installers. However, it generally takes longer than vinyl siding installation.
Is fiber cement insulated siding susceptible to mold and mildew?
While resistant, proper ventilation and occasional cleaning can prevent mold and mildew growth, especially in humid climates.